Top Rated Products
Our Most Popular Categories
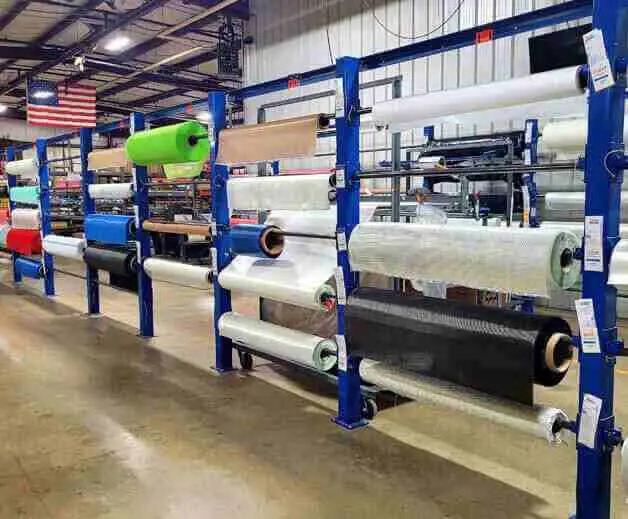
Welcome to Fibre Glast
Fibre Glast Developments has specialized in the distribution of fiberglass and composite materials for over 50 years.
In this time, we've built the largest and most comprehensive composites catalog in the industry; investing along the way in the product knowledge to support it. That means you can depend on Fibre Glast as a trusted and reliable resource for all your project needs.
What's more, professionals look to Fibre Glast to deliver composite materials that are always First Quality. With an ISO Certified Management System in place, we work to ensure that our products meet the highest quality specifications, and that they are supplied to you promptly and with consistent characteristics each time you order. There is no exception.
At Fibre Glast, we want your project to be a success, whether you're a beginner or an expert. And we're equipped to get you moving in the right direction. Let us know how we can help you.